

In particular, the ability to reconfigure a material into a new shape, without building a new part, would contribute significantly to the recyclability and sustainability of the system. Materials that can be configured and reconfigured multiple times into different shapes with the use of different stimuli could revolutionize manufacturing processes. With the introduction of the appropriate environmental cue, these materials can be driven to controllably change their shape, and thus, their functionality. 1,2 To achieve such reconfigurability, the printed materials typically encompass stimuli-responsive components. Introduction The aim of 4D printing is to create materials that can dynamically alter their morphology, and hence, time becomes the fourth dimension that characterizes the structure of the material. On a conceptual level, our results provide guidelines for combining different types of stimuli-responsive components to create adaptive materials that can be controllably and repeatedly actuated to display new dynamic behavior and large-scale motion. The findings thus reveal the distinct advantage offered by these hybrid materials: a single composite yields access to a range of dynamic responses and structures. These studies provide insight into the complex mechanisms by which multiple stimuli interact with an adaptive material to produce different forms of reconfiguration and actuation. Via our model, we uncovered the cooperative interactions that control the reorganization of the responsive fibers and the morphological changes of the gel in the presence of light, heat and the combination of the two stimuli.
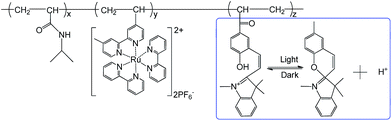
The complexity and potential functionality of the material is, however, increased when the fibers are also stimuli-responsive and thus, constitute active elements. If the fibers were passive elements, the materials would already exhibit valuable attributes, with the strong fibers acting as a skeleton that reinforces the “muscle” provided by the responsive, active gel. Conceptual insights Using computational modeling, we designed new, physically-realizable composites that integrate functionalized, photo-responsive fibers with thermo-responsive gels. Overall, our results point to a robust method for controllably reconfiguring the morphology of compliant composites and amplifying the effects of external environmental cues (light or temperature) on the behavior of these systems. Hence, our findings indicate how a given sample can be fashioned into different shapes through the use of separate stimuli. Common to both the tethered and untethered samples, one material displays a distinct response to the different stimuli. When the sample is detached from the surface, then the composites shrink like an accordion when heated and bend like a caterpillar when illuminated. In particular, samples anchored to a surface bend in one direction when illuminated and in the opposite direction when heated. When the SP-functionalization is confined to fibers that are embedded in the gel, the material displays distinctly different behavior in the presence of light and heat. If these chromophores are uniformly distributed in this LCST gel (without the embedded fibers), then both light and heat produce the same effect on the sample, causing the gel to undergo a uniform collapse. The elastic fibers are functionalized with spirobenzopyran (SP) chromophores, which become hydrophobic under blue light. The gel displays a lower critical solution temperature (LCST), and thus, shrinks at elevated temperatures. As a step toward creating such useful, adaptive materials, we use computational modeling to design a composite that integrates a thermo-responsive polymer gel and photosensitive fibers. Materials that could be reconfigured multiple times into different shapes with the use of different stimuli could dramatically impact manufacturing processes.
